Abstract 摘要
基于生物经济的建立已被公认为实现可持续发展的关键问题之一。对于未来的发展,可再生能源将发挥二氧化碳中性原料的重要作用,为可持续工业生产,遏制化石资源的枯竭。选项作为工业化工原料意味着不同的相互依赖的路线充分利用可再生资源的潜力。石化行业的方法如下:对于每一个场景中,宏图三胞的做法是必要的。各方面都需要从粮食安全,食品安全,“绿色”能源生产和可持续的非食品类产品为产业的发展,给废物管理,回收和处置。新兴战略需要相结合,从科学和商业企业的努力,通过政府立法,促进并应基于广泛的公众支持。2004年保留的爱思唯尔B.V.所有权利。Establishment of a bio-based economy has been recognised as one of the key issues for sustainable development. For future developments renewable resources will play a key role as CO2 neutral raw material for sustainable industrial production to curb depletion of fossil resources. Options to fully exploit the potential of renewable resources as industrial chemical feedstock imply different interdependent routes. In this paper, the various scenarios how to achieve a bio-based economy are discussed, ranging from the traditional ‘complex route’ via chemical conversion, to shifting to a glucose-based economy (C6) or transformation of biomass into C1 or C2 chemical building blocks, following the approach of the petrochemical industries. For each scenario, an integrated chain approach is essential. All aspects need to be addressed from food security, food safety, ‘green’ energy production and development of sustainable non-food products for industry, to waste management, recycling and disposal. The emerging strategies require combined efforts from both science and commercial enterprise, facilitated by governmental legislation and should be based upon a broad public support. . 2004 Elsevier B.V. All rights reserved.
1. Introduction 介绍
可再生资源替代对化石产品似乎恢复的,因为他们的取之不尽,用之不竭的可用性,并要考虑环境因素,如对生产的温室气体(CO2封闭循环)和潜在的碳汇中性偏好。许多国家的政府正在考虑一项政策,建立一个基于生物经济(如美国农业部,2000;克林顿,2000年的报告),其中可再生产品的开发设想一个可持续发展的社会的发展。在这样的政策有明显的选择是基于植物的原料,以促进可持续(化工)产业的发展。在工业中使用的农产品原料是不是新的。相反,即使是引进农业前,男子使用的植物资源,以掩盖他对能源,服装,工具,住房和药品(斯佩尔曼,1994;哈代,2002年)的需求。只有在前面的0926-6690 / $ - 见前面的问题。 2004年保留的爱思唯尔B.V.所有权利。 DOI:10.1016 / j.indcrop.2004.02.003Renewable resources as alternative for fossil based products seem to regain preference because of their inexhaustible availability and due to environmental considerations such as neutrality towards production of greenhouse gasses (closed CO2 cycle) and potential carbon sequestration. which envisages development of a sustainable society by the exploitation of renewable products. In such a policy the obvious option is to promote development of sustainable (chemical) industries based on vegetable raw materials. The use of agricultural raw materials in industry is not new. On the contrary, even before the introduction of agriculture, man used plant resources to cover his needs for energy, clothing, tools, shelter and medicines (Spelman, 1994; Hardy, 2002). Only in the preceding 0926-6690/$ – see front matter . 2004 Elsevier B.V. All rights reserved. doi:10.1016/j.indcrop.2004.02.003 #p#分页标题#e#
J.E.G. van Dam et al. / Industrial Crops and Products 21 (2005) 129–144 half-century the technologies were developed to substitute non-food uses of agricultural raw materials for fossil resources on large scale. Turning the tide in favour of renewable resources will have serious consequences for the demand on raw materials and supplies. However, the economic circumstances for primary production of agricultural raw materials are a limiting factor, especially in Western Europe, due to high costs for land, labour and investment. In a densely populated country like the Netherlands agriculture has to compete for land use with space for living, nature development and recreation, transport and industry. Globally the conservation of valuable landscapes, habitats, biodiversity and resources, as well as the need for socially responsible entrepreneurship have become relevant considerations in land use, environmental planning and strategic agricultural developments. It can be expected that the areas reserved for arable and dairy farming will further decline, while the demands on food quality and food safety will increase. A higher productivity per hectare has to be realised with better efficiency of resource use while also the sustainability of the whole production chain needs to be improved. The only way to overcome these barriers is to make a “quantum-leap” towards a bio-based economy (Jansen, 2000). This requires a joint effort from the agricultural sector, (chemical) industries, governments and consumer and user organisations, fully utilising the available scientific infrastructure and multidisciplinary expertise. Therefore, there is a need to identify suitable and reliable biomass raw materials for conversion into commodity products substituting fossil resources. The technological innovations for biomass conversion, that substantially contribute to CO2 emission reductions and that are economically viable, require strong promotion and deserve full political support. Such a strategy for enhanced utilisation of renewable raw materials derived from plant products obtained from agriculture or forestry should therefore be built upon realistic scenarios, matching potential supplies and future needs. Corner stones for the foundation of such a strategy are indicated and the major barriers for further progress will be indicated in this contribution.
2. Biomass: a renewable resource 生物质:可再生资源
Raw materials of vegetative origin can be roughly divided into common primary metabolites, secondary metabolites, and plant-derived products. Primary metabolites are used to generate and store energy (oil, starch/carbohydrates, protein) or to provide structural integrity (lignocellulose fibre). Secondary metabolites are specifically found in higher quantities in certain crop species and can be used to produce speciality products and fine chemicals such as dyes, aromas, flavours and medicinally active compounds. Plant-derived products may be obtained by fermentation or chemical conversion of biomass (e.g. ethanol, acetic acid). In the last decades crop diversification has been one of the promises for European agriculture. As a result of surpluses in the production of the major food crops (sugar beet, cereals and potato), which has arisen from increased productivity, alternative crops for non-food markets have received substantial interest (Van Dam and Elbersen, 2003). However, large-scale cultivation of non-food/non-feed crops has been declining world-wide for many different crops in the past decades (e.g. flax, jute, castor, poppy, madder, etc.) since the introduction of cheap synthetic (petrochemical) alternatives after WW II (FAO, 2002). However, a number of products with unique properties have been able to withstand successfully the severe competition of synthetics, such as wood for timber and paper pulp and cotton for textile fibre. #p#分页标题#e#
3. Bio-based economy and sustainability 生物经济与可持续发展
As the world population will keep growing also the demand for food, energy and raw material will steadily grow. Combined with the need to strongly reduce emissions of greenhouse gasses in the coming decades, consequently a bio-based economy should emerge in the near future (Shell Int., 2001; Clinton, 2000 Report). Renewable resources have potential as alternative raw materials for (chemical) industries, provided that ecologically sound agricultural production and processing technologies are available and applied. Feeding the growing world population in the coming decades requires production of some 109 Mg of biomass (yielding 0.3 × 109 Mg of food).
J.E.G. van Dam et al. / Industrial Crops and Products 21 (2005) 129–144 Scenarios for shifting to a bio-based economy calculate a demand of another 109 Mg biomass for energy production, equivalent to 160 EJ, supplying approximately 15% of the projected energy demands in 2050 (Shell Int., 2001) and 3–4 × 109 Mg of timber and fibre for building and 2 × 109 Mg for production of chemicals and specialities. This will require enormous and coherent changes in primary production, logistics and processing technologies. Only an integrated approach will lead to effective utilisation of the available biomass for food and non-food as well as energy. Changing to a bio-based economy requires substitution of many common raw materials that are currently largely produced from fossil (petrochemical) or mineral resources, by products produced from renewable (plant-based) resources. Development of a sustainable global economy, which permits improving purchasing power and living standards without exhaustion of resources for future generations, requires a fundamental change in attitude. On ecological grounds products should then be preferred that are based on photosynthetic CO2 fixation. The benefit of those sustainable resources is that they can be regrown within the foreseeable future, without negative side-effects on global bio-diversity. Therefore, competitive products based on renewable resources need to be developed that have high quality, show excellent technical performance and harm the environment less than current products based on petrochemical materials.
3.1. Linking of markets
The market development for sustainable raw materials requires integration of the numerous links in complex production chains. Food product markets are well defined and the production chains are well established. Valorisation of by-products, residues and waste streams, however, requires more attention. According to the principles of whole crop utilisation and integrated plant conversion, residues coming from food production and processing can be valorised by various scenarios into fuel or by bio-cascading or bio-refining into raw materials for chemical industries (Fig. 1). Non-food production chains can roughly be ranked based on increasing added value: energy, bulk chemicals, building and construction materials, fine chemicals, textiles to pharmaceutical products. The renewable raw material supplies should match the market demands according to product type, pricing, quality and quantity (Fig. 2). The development should, in principle, be starting from the market demand and search for supplies of the fitting raw material and conversion technology (chemical, physical, and/or biotechnological). Subsequently, organisation of the sustainable agricultural production chain and planning of land use then come in the picture. Vertical integration, i.e. optimal design of the value chain by combining markets for food, energy and non-food, is needed because the use of biomass products always involves several more or less independent chains: sustainable exploitation of biomass can only be realised when all flows of products and residues are allocated to uses that guarantee maximum value (De Klerk-Engels, 2002). The ‘green’ energy chain will be the driving force for the development of added value products (Fig. 3). Basically, therefore, it is required that biomass conversion into energy not only involves the relatively inefficient thermal conversion to electrical power (co-burning), but also the production of (liquid) transportation fuels (e.g. ethanol, methane, bio-diesel, hydrogen) (IEA Bio-energy, 2003). The biomass resources can be of very different composition and be available in variable amounts. It may be derived from municipal solid waste, conventional and short rotation forestry, agricultural residues or bio-energy crops, and oil crops. Biomass never represents a pure chemical component and the complex product is composed of various amounts of water, carbohydrates, lignin, proteins, and many other organic constituents. Often it is also contaminated with other materials. Therefore, it requires refining and extraction to enhance the product value. Harvesting, collection and handling of the biomass should be adapted to the intrinsic properties and the conversion process. Preconditions for suitable biomass conversion technologies require a system change, turning residues and waste into valuable products. The technology should be not fastidious, but robust and flexible with respect to input feedstock, and reliable in its product output. Moreover, it may be available in seasonal peaks. Decision support systems are required to streamline the flow of input raw material and output product according to the balance of supplies and demands of the market. #p#分页标题#e#
J.E.G. van Dam et al. / Industrial Crops and Products 21 (2005) 129–144
Fig. 1. Coherence of food and non-food markets and the necessary development of the non-food production chain.
3.2. Conversion routes for biomass
Traditionally a crop was selected and grown for its most valued component: wheat for grain, flax for fibre and potato for its tuber, etc. With the change to a bio-based economy in mind, this approach cannot lead to sustained economic developments and new routes need to be taken. The whole crop utilisation by complex bio-cascade or -refinery systems has been considered in the last decade and several options to expand the agro-industrial potential for raw material supplies have been investigated. Integrated plant conversion or bio-refinery systems require process innovations, which will be similar for various chains based on different sources of biomass (grasses, potato foliage and peels, sugar beet pulp, etc.). Adaptations will be required starting at the primary production level, including modified crop handling and on-farm pre-processing. These innovations involve extraction technology, fermentation and/or chemical conversion, de-watering, desalting, etc. Also logistics of raw material supplies require detailed attention, dealing with
J.E.G. van Dam et al. / Industrial Crops and Products 21 (2005) 129–144 3000€/Mg 2000 1000 0 Agricultural production Fibre production Textile fibre Cellulose Non-woven Pulp Geotextiles Fourage Animal bedding Energy Compost Fibre crops Agro residues Waste biomass Energy crops Market Production costsAdded value Conversion steps
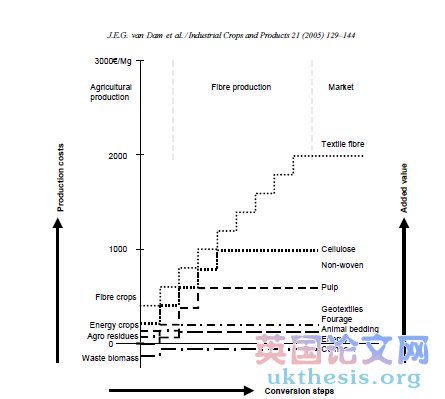
Fig. 2. Value addition of fibre crops in the agro-industrial production chain. aspects such as seasonal variation in quantities and qualities, effects of storage on the product, cheapest means of transport. The seamless connection to market sales demands robust and flexible conversion technologies and huge depot buffer capacities, but also strict quality control and alternative outlets for rejects. The various routes and approaches are described here, including a brief overview of new routes for biomass conversion (C6 route and C1/C2 route), that fit in the current practice of petrochemical industries to convert crude oil by several steps into small chemical building blocks, from which a wide range of chemicals are produced.
3.3. Constraints
The high investment costs and risks for industries to convert the existing large-scale production to utilising alternative resources, requires compelling arguments and profitable perspectives. For example, the use of hemp pulp in paper industries would require investments of several million , which seems unrealistic when a positive balance of 2.500 is requested per hectare for agricultural production (Bakker and Van Kemenade, 1993). Due to drastically changing paper properties made from hemp bast fibre, and reduced processing efficiency, the market for expensive hemp pulp is restricted (De Groot et al., 1999). Only small specific niche markets may have commercial prospects for hemp pulp given the severe competition of large-scale production of paper pulp from wood and recycled paper. Therefore, it is difficult to achieve alternative supply chains for industrial crops and new agricultural products supplying an existing bulk market on the short term and under actual economic conditions. But nevertheless also the existing #p#分页标题#e#
J.E.G. van Dam et al. / Industrial Crops and Products 21 (2005) 129–144 Biomass modificationprecipitation coating extract sugars commodity chemicals effluent drying cutting pelletising residue fodder dump extraction protein gasify incineration energy waste compost composting silica fermentation tar ash fuel refining pulp paper
Fig. 3. Biomass conversion scheme. production chain of, for example, flax linen and emerging production of fibre composites requires reconsideration.
4. Examples of the ‘complex route’ “复杂航线”的例子
The use of renewable resources as industrial feedstock for manufacturing of chemicals and products has received much attention in the past decades. Substitution of fossil resources can be achieved to some extent by extraction of oils from oilseed crops, cellulose from straws and wood, starch from cereals to produce a range of polymers, lubricants and chemical intermediates. In this section, examples of this approach are described as examples of the lessons learned in these sectors with innovations and novel product development.
4.1. Fibre production chain
4.1.1. Markets of fibres, existing and new applications For competitive West European agricultural production of fibre crops, it is essential to supply high quality grade raw materials with an added value for the end-user (Van Dam et al., 1994; Van Dam, 1999). Severe competition from cheaper fibres that are available in bulk quantities (i.e. jute and sisal) and the potentially large scale production in Eastern Europe of flax or hemp has forced the agro-industrial production in the EU into a specialised niche market. Traditionally, the flax fibre production in Western Europe for high quality linen has been able to cope with competing imported raw materials, because of its high standard of quality. The flax-linen production chain is composed of many labour intensive steps in which the intermedi
J.E.G. van Dam et al. / Industrial Crops and Products 21 (2005) 129–144 ate products are handled with utmost care to maintain the high fibre quality standards. The production scale and market price of linen fibre is dominated by the demand of the strongly fluctuating fashionable textile market. Revenues obtained from linen textiles should cover the main costs of the whole long fibre production chain (Fig. 2). Many novel end-uses for cellulosic fibres have been identified (Van Dam et al., 1994) and demonstrated to be technically feasible. The lower qualities of fibre (flax tow and straw), which are produced as residue from agro-industrial production have to compete with cheap wood fibre on the market for paper and pulp, fibre board and composites. Both hard-and soft-wood fibres are utilised on large scales for refining and pulping. Only about 11% of the world’s virgin cellulose pulp is made from non-wood sources (mainly straw, bagasse, and bamboo). In the EU, US and Canada practically no non-wood pulp is currently used (De Groot et al., 1999). The use of cellulosic fibres as renewable raw material in fibre reinforced composite materials is receiving much attention in the automotive industry and shows much promise (Wotzel et al., 1999; Schl..er and Knothe, 2000). Flax and hemp non-woven find a growing outlet in compression moulded trim panels and dashboards, because of weight reduction and easier recycling by incineration. Another potential market for ligno-cellulosic materials is found in an increased interest for renewable materials in building and construction applications. However, complex building regulations and standardisation in the different EU member states, combined with different legislation on the use of building materials at national levels, make the introduction of novel products on this scattered and conservative market difficult. Implementation of alternative renewable building products at large scale involves substantial commercial challenges that should be the driving force behind development of the production chain. This can only be achieved when the qualitative and quantitative aspects have been defined in detail for each specific end-use. It should be substantiated that especially in the case of building materials, the ecological advantages should combine with better comfort, health and safety aspects (indoor climate), without premature degradation or excessive maintenance costs or the need for hazardous chemicals for preservation. #p#分页标题#e#
4.1.2. Production chain
During the various steps of fibre production from agricultural raw materials, many factors influence the final product quality. Each stage in the production chain affects the value of the end product. Depending on the required performance of the fibre in the end-application, the production and processing costs determines its economic feasibility. There are big differences in quality demands and economy between the specialised production of flax textile fibre, specialised energy crops (Miscanthus, switch grass) or valorisation of agro-residues (wheat straw, corncobs). The production chain for fibre crops can be divided into three main links: agricultural production, fibre processing, and utilisation (Scheme 1). Despite interdependency of the different links in the chain, interests may be divergent with respect to quantitative and qualitative aspects. As long as primary production is paid for quantity rather than quality, breeding will focus on yield improvement. Objective rating systems are a necessity to appreciate quality. Therefore, it is important to develop a certified fibre production chain, using instrumental and predictive methods as standards of qualification. This is especially relevant for the novel industrial end-uses like composites or building materials. Each application, however, will have specific demands on the performance of the raw material, which may be confidential industrial information. The quality control in the fibre production chain is requiring much attention and geared activities of all parties concerned (Van Dam, 1999). The low-end market outlet for fibrous biomass is found in energy production (Fig. 2). Promotion of renewable energy and biomass conversion plants by the various European governments is targeting for a doubling of the contribution to the energy production over the next 10 years. It should, therefore, increase from below 2% of the total energy consumption now to over 10% in 2020 (Dutch Govt policy targets). Since biomass utilisation for energy production is still expensive, compared to fossil energy sources, the so called ‘complex route’ or cascade principle is considered. Combined fibre extraction and energy production may increase the revenues.
4.1.3. Economics of fibre crop production
Minimum costs of production for fibre flax in the Netherlands (Kasse, 2002) by traditional methods of J.E.G. van Dam et al. / Industrial Crops and Products 21 (2005) 129–144
Scheme 1. Agro-industrial chain of fibre crop production, processing and application. The interdependent links influence the end product price and performance. harvesting (pulling and dew retting) and processing for textile fibres, have been calculated to amount over 3000/ha. With an average yield per hectare of 8 Mg straw, the minimum straw price for the farmer should then amount at least 380/Mg in order to be profitable. Adding to the production costs of linen textile fibre are the different specialised tools and equipment designed for parallel aligned harvesting and processing of fibre flax. The crop per hectare will be yielding on average 1 Mg of long fibres, 1 Mg of short fibres (tow), 3 Mg of shives and 1 Mg of linseed #p#分页标题#e#
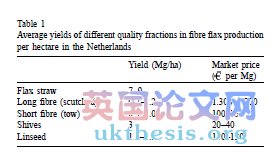
(Table 1) bringing globally an income below 2000/ha (including costs of deseeding and fibre extraction processes; scutching equal to 115/Mg). The gap between production costs and market value of the raw materials has been bridged in the past decades by EU financial support, but the EU support regulations for fibre production have been changed dramatically. The economic production of flax in the EU without subvention will become impossible if the yields and/or market prices do not increase. If this Table 1 Average yields of different quality fractions in fibre flax production per hectare in the Netherlands Yield (Mg/ha) Market price ( per Mg) Flax straw 7–9 Long fibre (scutched) 0.7–1.2 1.300–1.700 Short fibre (tow) 0.4–1.0 100–150 Shives 3 20–40 Linseed 1.1–1.5 150–190 market is to be maintained, primary production has to shift to cheaper production areas. Stimulation of alternative market outlets with a more efficient production chain, however, could even enhance economic activities. These markets for fibre products then should be identified between the value added textile market and economic value of energy from biomass (Fig. 2).
4.1.4. Economics of energy crop production
At the low end of the fibre production chain the utilisation of fibrous biomass for its energy content has received much attention. Ligno-cellulosic fibres, ranging from agro-industrial waste biomass (biomass from road verges, food crop residues, processing wastes, pruning wood) to energy crops like Miscanthus, Phalaris or switch grass, have been studied for their potential as source for the production of ‘green energy’ (Van Dam et al., 2000; Elbersen et al., 2000; De Vrije et al., 2002). The negative economic value for costs of waste disposal makes valorisation of voluminous waste streams attractive. Large variation in composition and contamination complicates combustion and requires development of flexible processing units for control of tar and ash formation. Due to the seasonal variation in supply, a highly organised logistic chain needs to be set up. When the price for crude oil remains around the level of US$ 15 per barrel, bio-energy production cannot compete cost wise without governmental intervention. For generation of energy 1 Mg oil (~ 100) is then equivalent to approximately 3 Mg of ligno-cellulose raw materials (dry matter, e.g. straw).
J.E.G. van Dam et al. / Industrial Crops and Products 21 (2005) 129–144 High yielding energy crops may provide 15 Mg dry matter per ha and thus an income of ~ 500/ha, which should balance the cost of production. In the case of agro-residues like wheat straw, which may yield 3–8 Mg/ha, valorisation of surplus straw as fuel is adding at least 100/ha. Straw in other uses (animal bedding and horticultural use) has a market value up to 60/Mg. To make the production of biomass profitable, additional income has to be generated, for example by cascade utilisation of cellulosic fibres and recycling, valorisation of residues (silica and tar) (Fig. 3). #p#分页标题#e#
4.2. Biocascading
Recently much effort has been put into the biocascading concept for whole crop utilisation (Rexen and Bagger, 2002; Bagger et al., 1999). In this scenario not just one crop is grown for one product, but by means of a number of sequential steps by direct extraction (separation and isolation followed by conversion and derivatising), indirect extraction or conversion (e.g. through thermal or thermo-chemical and fermentation processes) and residue conversion (e.g. incineration) a number of products can be generated with various economic value (Struik et al., 2001). Examples are the bio-cascades for sugar beet, hemp and grass (De Wilt et al., 2000; NOVA Inst., 1996). Although this concept is not new, this strategy offers a better perspective. Strong points are that the
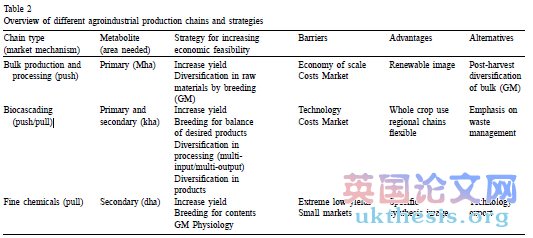
Table 2 Overview of different agroindustrial production chains and strategies total biomass is being harvested and utilised and the economic feasibility is not solely dependent on a single market (Table 2). In extreme cases biomass of different origin (waste, agro-residues and surplus crops) can be fed by means of multi-input/multi-output systems into the different stages of the bio-cascade and yield (by)products with some economic value. In this way bio-cascading may become more economically attractive (up to 100% application of the crop) and also contribute to waste processing. The breeding and agricultural production no longer need to be focussed on one specific application and the technology can be improved in such way that also other flows of biomass can be exploited. Flexibility is a great advantage, but the chain should be locally oriented. The required area for a processing unit amounts thousands of hectares within a radius of 10 km. This implies development of rural employment in the primary production areas. The raw material production potentially may take place alternating with valuable cash crops, but also on large extensive farms with reasonable land prices. Processing technology, however, still requires optimisation (Struik et al., 2001).
4.3. Speciality crops
Many plant species synthesise so called secondary metabolites, compounds that occur only in small amounts and play a specific role (such as signalling compounds and terpenes) in the plant. Those Chain type (market mechanism) Metabolite (area needed) Strategy for increasing economic feasibility Barriers Advantages Alternatives Bulk production and processing (push) Biocascading (push/pull) Primary (Mha) Primary and secondary (kha) Increase yield Diversification in raw materials by breeding (GM) Increase yield Breeding for balance of desired products Diversification in Economy of scale Costs Market Technology Costs Market Renewable image Whole crop use regional chains flexible Post-harvest diversification of bulk (GM) Emphasis on waste management processing (multiinput/multi-output) Diversification in Fine chemicals (pull) Secondary (dha) products Increase yield Breeding for contents GM Physiology Extreme low yields Small markets Specific synthesis image Technology export #p#分页标题#e#
J.E.G. van Dam et al. / Industrial Crops and Products 21 (2005) 129–144 compounds can be of great value as health care products to man, as they can be used as natural flavours, fragrance, medicines (drugs and vitamins), dyes, biocides and repellents. The demand for those fine chemical compounds is market driven (pull). Those compounds often have complex chemical structures and are only produced by a small number of plant species by means of complex biosynthetic pathways. Those compounds are often hard to obtain by organic chemical synthesis in the laboratory. Although many have successfully been mimicked in the laboratory, industrial production often still relies on the natural product (e.g. salicylic acid, vanillin and morphine). In those cases the proposed scenarios of bulk production or bio-cascade fail. Sometimes synthesis of such compounds by microbial fermentation is a possibility after genetic engineering and sometimes cell tissue culture production is successful. But in most cases agricultural production is the only option. Depending on market and product value it is feasible to perform breeding and growth optimisation. Much progress can be made by study of crop physiology and agronomy (Struik et al., 2001). The market volumes of those products are generally limited. Exceptions can be compounds that are cosmetic ingredients (perfumes) or effective medicines against common diseases such as malaria and cancer. When the contents of the secondary metabolites are low (e.g. artemisinin in Artemisia annua or taxol in Taxus sp., morphine in Papaver, and many more) substantial areas may be required and the successful organisation of an efficient production chain (including breeding, seed production and industrial processing) may be a possibility. But even in those cases a maximum of several dozens of hectares are required up to some thousand hectares. Due to the specialised character and the high price (e.g. up to 6000/g for taxol (Hess, 1998) cultivation can be performed on expensive land, preferentially in the vicinity of primary processing and to the further production agro-industrial chain, at least when the ecological circumstances permit so. Only in such case the old approach of growing a crop with only one target is suitable. Also, for the discarded biomass after extraction, bio-cascading will be the option for enhanced sustainability (Struik et al., 2001). Alternative cheaper production of those special products will be the challenge for biotechnological production systems to become competitive on this market.
4.4. Other non-food use of starch, proteins and oils
Similar examples of industrial non-food products are derived from the starch industries finding outlets in thermoplastic starch or modified starches as processing aids and additives in paper production and adhesives. Also, plant oils—whether or not chemically modified—are widely used in industries as coatings, lubricants (hydraulic oils, motor and gear oils, etc.), surfactants, bio-fuel and linoleum. Soybean proteins have been explored for similar industrial non-food uses (Spelman, 1994; Sessa and Willett, 1998)by chemical cross-linking and modification. The potential market share of renewable based products in the EU is expected to increase substantially by 2010, especially for the consumption of surfactants, lubricants and solvents. For such development EU legislation on waste oil disposal and solvents will be critical (ECCP, 2000). #p#分页标题#e#
4.5. Multipurpose crops
Plants that produce oilseeds or starch generally are being produced for this primary product. However, the utilisation of the biomass residues of oilseed flax, wheat straw, rice husks or corncobs, would increase the revenues per hectare. In the past breeding trials for dual-purpose crops (e.g., both fibre and oilseed production from flax) have failed, which is partly due to the intrinsic incongruous events of fibre production and maturation on the one hand and seed production and ripening on the other hand. The technical potential of multi-purpose use of different plant parts will require optimised harvesting and crop processing to yield the highest added value or providing maximum supplies for bulk outlets. For efficient extraction of valuable components in complex mixtures advanced technologies need to be developed.
4.6. Transfer of technological successes
In the past decade a number of technological innovations based on agricultural products have been elaborated, following the strategy of the ‘complex
J.E.G. van Dam et al. / Industrial Crops and Products 21 (2005) 129–144 route’. In addition to non-textile fibre crop application developments in biodegradable geotextiles, building insulation, horticultural substrates and cellulose fibre reinforced composites, numerous other crops have been investigated (Van Dam and Elbersen, 2003). Examples of technological achievements are products based upon thermoplastic starch, carvon as sprout inhibitor in potato storage, calendula-oil in coatings, oilseed rape and sunflower oils for lubricants and hydraulic fluids, soybean proteins in adhesives, and plant dyes (such as madder and woad) in textiles. Some of the research results have been transferred to industrial production and have already been successfully commercialised in a relatively small niche market. Some are on the verge of a larger breakthrough. Others may still require more development. The EU legislation restricting volatile organic solvents in paints, coatings and adhesives for professional use, has increased the demand for specific plant oils. However, higher costs and reduced practical value restrict more common use of ecological products.
5. Chemical conversion 化学转化
5.1. Cellulose
A good example of a bio-based chemical industry is found in the cellulose industries. The abundantly available raw material has made production competitive. It is estimated that annually 1011 Mg of cellulose is produced by biosynthetic conversion of CO2 in biomass fixation. Only a small part is being utilised by mankind. The annual world consumption of about 150 × 106 Mg of cellulosic fibre is mainly commercially used for the production of paper, textiles or chemical-grade cellulose. On top of that 109 Mg of wood (consisting of almost 50% cellulose) is consumed for fuel and lumber. Semi-synthetic cellulose derivatives such as viscose/rayon, carboxymethyl cellulose (CMC), cellulose acetate (CDA and CTA) and a number of other ones are commercially exploited on large scale. However, cellulose acetate as a thermoplastic polymer with excellent properties cannot compete on the commodity markets for polyolefins (polypopylene (PP), polyethylene (PE)), because of scales and price. #p#分页标题#e#
5.2. Lignin
Lignin is the second most abundant biopolymer on earth. Approximately 50×106 Mg lignin is being produced per year world-wide as residue of paper pulp production. The major part of the residues from chemical pulping extraction processes of cellulose from wood is not utilised. In the closed recovery boiler systems of the modern pulp mill, after evaporation of huge amounts of water, the organic fractions in the black liquor are burned for generation of processing power. The black liquor is composed for a substantial part of lignin. Only a small part of this finds commercially application yet. Several factors of influence can be appointed to this lack of success, from the smelly image as a waste product and inhomogeneity of lignin sources to the lack of supply and investors. Barriers to overcome for enhanced utilisation of lignin products involve the identification of competitive outlets and efficient conversion processes leading to reproducible and stable supplies of renewable phenolic chemicals. Large numbers of patents have been filed for use of lignin and lignin derivatives, so far only commercialisation of ligno-sulfonates, obtained from the sulphite pulping process, has been a success (Gargulak and Lebo, 2000). Lignin chemistry could be considered as a separate route (C9 chemistry).
6. ‘C6 route and C1/C2 route’: new strategies in crop production and handling C6路线和C1/C2路线”:在作物生产的新策略和处理
6.1. Bulk crop production
The strategies for (re)introduction of industrial crops have been oriented towards bulk production of a crop or raw material such as rapeseed for bio-diesel or hemp for fibre. The crop choice stems from the desire to supply a certain market, even though this market still requires to be developed or penetrated (market push). This strategy is bound to fail. Bulk product prices on the world market for those commodities are too low for agricultural production to be competitive. Even the creation of added value does not help to overcome these barriers due to adverse effects of production scale. Breeders of oil crops have been successful in changing the composition of fatty acids (Downey, 1992), however those cultivars are
J.E.G. van Dam et al. / Industrial Crops and Products 21 (2005) 129–144 not grown at substantial scales because breeding, cultivation, storage and processing all require treatment separate from the current crop, which increases the costs of each link in the production chain, without the much higher yields or profits. Therefore, bulk production of agro-raw materials can be better performed in areas with cheap land and labour for large-scale extensive farming in combination with creation of product diversification at the end of the production chain, utilising micro-organisms or enzyme technology. This is considered as the C6-route for biomass conversion. For this route, only extremely efficient industrial crops producing mainly carbohydrates, composed of C5 or C6 monosaccharide building blocks (sugar cane, sugar beet, low-lignin fibre crops) may be utilised (Struik et al., 2001). Theoretically, the conversion steps can be performed bio-technologically at the end of the production chain by micro-organisms or enzymes. The basic raw material should be sufficiently biologically and/or chemically specific for simple conversion and application in chemical industry. The demand for agricultural production area amounts millions of hectares, while the product price paid for primary carbohydrate raw materials will be only some 20–30/Mg. #p#分页标题#e#
6.2. Carbohydrate fermentation
In contrast to the value chain approach or “complex route”, in which the identified value added products are isolated from the biomass and the remaining residue is considered for transformation with a bio-cascade system, another concept of biomass conversion would be an integrated chain approach, analogous to the common practice in petrochemical industry. The crude substrate is converted into universal building blocks that are used to produce a variety of chemical intermediates, polymers and products (Van Tuil et al., 2002). 6.2.1. Glucose for chemical intermediates Chemical or biochemical hydrolysis of starch or cellulose will yield glucose that can easily be fermented and converted to valuable products, such as in the case of polyols and bio-based polyesters (PLA and PHA). Sugar based chemicals such as sorbitol are used as chemical intermediates, with a range of applications. Similarly, hydrolysis of crude polymeric carbohydrates in biomass to pentose (C5) and hexose (C6) monomers and further conversion to C1 or C2 chemical building blocks, would offer the technological and economical advantage of efficient production in highly integrated facilities. Transformation of biomass into commonly applied building blocks used in petrochemical industry is the main technological challenge. Therefore, efficient conversion technologies of heterogeneous biomass yielding reliable quantities of pure chemicals is a prerequisite. 6.2.2. Fermentation processing Ethanol (C2) production by fermentation from sugar has been one of the basic skills since ancient times of Epicurean civilisations. The option to transfer the technology into fuel production from molasses and waste carbohydrates has been implemented successfully on large-scale bio-ethanol production in Brazil as additive in car petrol. A number of other options to produce energy carriers by fermentation processes have been considered, such as methane (C1) and hydrogen (De Vrije et al., 2002). However, this is so far without large impact on the reduction of fossil fuel consumption. Of interest here is the quick expanding R&D field of ‘white biotech” for the production of (fine) chemicals by which the industrial biotechnology is designated. 6.2.3. Biotechnological conversion Xanthan gum is a good example of a commercially successful fermentation product. It is a microbial polysaccharide with specific gelling properties that is now widely used in food and oil-drilling industries. The present world-wide market for xanthan gum is about 50.000 Mg or 500 million per year. Other technological successes to be mentioned here are polyhydroxybutanoate (PHA) as plastic polymers from fermentation processes, and sorbitol derivatives as a substitute for phtalate plasticisers in polymer industries. In those cases a C6-approach can be recognised: the monosaccharides obtained from (crude) biomass residues are fermented or chemically converted into functional products. Renewable polyesters based upon biotechnological fermentation processes have been successfully produced and are currently being introduced to the market. Lactic acid obtained from carbohydrate fermentation can be polymerised into polylactic acid (PLA), a biodegradable polymer #p#分页标题#e#
J.E.G. van Dam et al. / Industrial Crops and Products 21 (2005) 129–144 with interesting properties and a scope for a variety of applications. At the end of all the biomass conversion chains anaerobic digestion/composting processes are the natural routes to degrade the residual products. Methane would be one of the useful end products, together with the compost that is widely used as soil improvement and fertiliser.
6.3. Thermal conversion technologies
The complex mixture of organic compounds present in biomass has a limited thermal stability. The major part will be degraded or converted at prolonged exposure to temperatures above 200 .C by a sequence of depolymerisation and rearrangement reactions. An example of thermal conversion in a value chain is utilisation of sugar cane bagasse and other agro-residues rich in C5 sugars, such as corncobs, chaff, etc. After acid hydrolysis of the biomass furfural is produced by dehydration in a digester under high-pressure steam. Furfural is a raw material for production of furan-based chemicals, which find application in renewable resins. 6.3.1. Pyrolysis and liquefaction Controlled thermal processing may yield a suitable raw material for chemical processing in an integrated chain. One promising feedstock could be bio-oil or the tar produced from liquefaction or pyrolysis of biomass. Currently, liquefaction and flash-pyrolysis technologies are being developed for conversion of biomass to produce liquid bio-fuel. Bio-oil is composed of a complex mixture of organic compounds, both aliphatic and aromatic. For fuel use as a liquid energy carrier the ratio oxygen/carbon is too high for use in present engines and hydrodeoxygenation would be required. This tar, however, may contain many useful products if only the technology would be available to recover and extract or convert it into more easy to handle fractions. 6.3.2. Hydrocracking In analogy with the petrochemical industry, the biomass is transferred by a sequence of refining, thermal conversion and chemical steps into ‘biocrude’, that is composed of small building blocks. Principally, the technology aims to remove the excess of oxygen in biomass at elevated pressures, which is liberated as CO2. Subsequently, the bio-crude is upgraded by catalytic hydrogenation to a diesel fuel substitute (Goudriaan, 2003). From this process numerous chemical products can be obtained as well and used for chemical synthesis of a range of products. 6.3.3. C1/C2 route Conversion of biomass into small units of one or two carbon atoms would fit in the highly integrated production facilities of the chemical industry. This would, however, require further depolymersation and conversion of bio-oil or -crude, of which the oxygen content has to be reduced by hydrogenation processes (Elliott and Neuenschwander, 1996). Gasification of biomass is yielding syn-gas, a mixture mainly consisting of CO and H2. This could become the future universal feedstock for both energy and chemical synthesis. Similarly, ethylene could be derived from biomass conversion. This C1 or C2 route approach fits in the current technological state of the art and infrastructure of the chemical industries. However, in petrochemical industries 97% of the crude oil is converted into energy and only 3% is used in chemicals and polymers. This balance may be quite different for biomass conversion. #p#分页标题#e#
7. New demands for industrial products 工业产品的新需求
A number of potential market outlets for bio-based products are being envisaged for the near future such as ‘green’ (block-co)polymers, starch based nano-particles, cellulosic micro-fibres, and chemicals with functional properties such as additives in polymer processing (UV-stabilisers, surfactants, plasticisers, fillers and colorants), adhesives, or coating. Chemical industry requires pure components for further processing. The production of synthetic polymers based on polymerisation of ‘green’ monomers requires high purification in bulk quantities of the organic compounds that can be derived from plant biosynthesis. Techniques to extract useful components from heterogeneous biomass require either a delicate approach or very robust handling. Efficient catalytic systems for chemical conversion of complex mixtures of organic compounds, e.g. hydrodeoxygenation, hydrocracking, processes for biocrude. The current supplies of renewable resources are based upon one of the conversion routes, either the
J.E.G. van Dam et al. / Industrial Crops and Products 21 (2005) 129–144 ‘complex route’ or the C6 and C1/C2 routes. However, those production chains are interlinked. For example, residues from C6 route, the carbohydrate fermentation, may be utilised as feedstock for the C1 route. Thermal conversion of non-fermented C5 carbohydrates may yield a good source for furan resins that may substitute phenolic resins for a large part. In future more of those technologies will become available for production of sustainable products for coatings, glues, cosmetics, pharmaceuticals, chemical additives, building materials, etc. However, there are barriers to overcome. Environmental arguments and a technology push are not decisive arguments for commercial successes. Limitations are being encountered in the scale of production. Often small companies do not have the marketing tools and financial resources to be competitive and successfully penetrate the market. Legislation and restrictions encountered in product (ISO) certification, quality control and supplies guarantees, etc. are often forming major barriers.
8. Conclusions 总结
8.1. Perspectives and conditions to be fulfilled to reach the aims Biomass will play a key role in the development of a sustainable economy.
The strategies and the long-term R&D targets require reconsideration. The cornerstones to build a bio-based economy that will be the basis whereupon a sustainable economy is resting, have to be formed by the complex of linked production chains and markets. The traditional ‘complex’ route and described scenarios for C5/C6 and C1/C2 require integration into a production chain that finds its drive in a market pull. Bulk production of millions of hectares is only feasible in Western Europe on large-scale extensive agricultural production areas on cheap land, growing only a few crops efficient in C5/C6 production with some biological and/or chemical specificity, followed by further diversification using microbial fermentation and thermo-chemical conversion (C1/C2). Cascading of biomass with different valuable components requires a smaller, regional oriented production chain. The accompanying technology however is still in development. Presently, it is rewarding only for the production of exceptional high priced fine chemicals to organise an agro-production chain for a single crop grown for one specific chemical including breeding seed production, growth and processing. Based upon an increasing market demand and a growing awareness of consumers, agricultural production of raw material seems to enter a new phase, under the umbrella of sustainable agro-industrial business development. #p#分页标题#e#
8.2. Research agenda Much concerted research effort will be required to reach the targets of a bio-based economy.
Starting from the primary production, agronomy and breeding research (including genetic engineering) will have to focus to enhance the efficiency of value added production chains. Much attention will be required for efficient design of phased agro-technological conversion processes, including extraction processes and separation technologies, that have to be versatile and robust, taking into account the potential added value of residues and aim for closed cycles and no waste production. Of major concern is the arrangement of supply chains, providing industries and consumers with the needed products of constant quality. Quality control at the various levels of production is subject of concern, demanding definition of standards and objective methods for evaluation. Of course innovation and product development is essential for commercial attractive products based upon renewable commodities. Industries should be encouraged to market ecologically improved products based upon sustainable production. Consumers should be offered attractive alternative products with good performance that can compete with existing market goods. The enhanced ecological performance of renewable products should, however, be demonstrated unambiguously by scrutinous analysis of the total life cycle of products. Much has been achieved over the last decade in the exploration of the potential markets for different fibre resources, although a real breakthrough still has to come. For example, as a renewable raw material fibre crops do have strong marketing arguments as ‘eco-efficient’ products for development of sustainable consumption and production. Diversification of the market for fibre products in automotive industry,
J.E.G. van Dam et al. / Industrial Crops and Products 21 (2005) 129–144 geotextiles, building and construction materials, paper and pulp, bioenergy, etc. are all feasible in the near future if the various market needs can be tuned to a versatile supply chain. The quality control of the agro-industrial production chain requires to be organised according to ISO-standards to guarantee supplies of specified products to industrial buyers. A number of aspects in quality control and improvement in the production chain of cellulosic fibres from agricultural produced fibres do need attention. In the whole life cycle of production and use—from breeding and primary production to combustion and disposal—the upgrading of quality and enhanced performance can be achieved by dedicated technology and logistic control systems. The R&D agenda for the chemical C1/C2 route will require much input to overcome the technical barriers for economic conversion processes of biomass to pure chemical building blocks that can compete with petrochemical derived components. Models for most efficient use of biomass resources and logistic decision support systems will be required to enhance the competitiveness and secure the future supplies of resources for industries. A multidisciplinary research and development approach is essential to bridge the gaps between the farmer and consumer. In contrast to the perspectives of the fourth rotation crop for EU-agricultural production outlined in the 1970s, which was not based upon a marked demand, the need for sustainable developments in the 21st century that reconcile growing demands for raw materials for industrial production, food needs and preferences for environmental quality should be given high priority on the research agenda. #p#分页标题#e#
References 文献
Bagger, C.L., Bjergegaard, C., S.rensen, H., S.rensen, J.C., S.rensen, S., 1999. High-quality oils, proteins and bioactive products for food and non-food purposes produced in pilot plant scale by biorefining of cruciferous crops. In: Proceedings of the 10th International Rapeseed Congress, Canberra, Australia. Bakker, H.J., Van Kemenade, M.J.J.M., 1993. Papier uit hennep van Nederlandse grond, eindrapportage van vier jaar hennep onderzoek: samenvatting, conclusies en aanbevelingen. Clinton 2000 Report: White House: The Executive Order (No 13134) “Developing and Promoting Biobased Products and Bioenergy”, ordered by William J. Alkaline pulping of fibre hemp. In: Ranalli, P. (Ed.), Advances in Hemp Research. Haworth Press Inc., pp. 213–242. De Klerk-Engels, B., 2002 Niet voedsel en groen. In: Koppeling van Kennis, p. 5–12. Uitgave Wageningen UR, The Netherlands. Downey, R.K., 1992. Biosafety of transgenic oilseed Brassica species. In: Proceedings of the Second International Symposium on the Biosafety Results of Field Tests of Genetically Modified Plants and Microorganisms, 11–14 May 1992, Goslar, Germany. ECCP, European Cliamte Change Programme, 2000. Liquid fuels by low-severity hydrotreating of biocrude. Dev. Thermochem. Biomass Conv. 1, 611–621. Elbersen, H.W., Christian, D.G., Bacher, W., Alexopoulou, E., Pignatelli, V., Van den Berg, D., 2000. In: Proceedings of the First World Conference on Biomass for Energy and Industry, 5–6 June 2000, Sevilla, Spain. Gargulak, J.D., Lebo, S.E., 2000. Commercial use of lignin-based materials. In: Glasser, W.G., Northey, R.A., Schultz, T.P. (Eds.), Lignin: Historical, Biological, and Materials Perspectives. ACS Symposium Series, American Chemical Society, pp. 304– 312. Goudriaan, F., 2003. Transportation fuels from biomass via the HTU process. In: Proceedings of the Fourth European Motor BioFuels Forum, 24–26 November 2003, Berlin, Germany. Hardy, R.W.F., 2002. The bio-based economy. In: Janick, J., Whipkey, A. (Eds.), Trends in New Crops and New Uses. Proceedings of the Fifth New Crops SymposiuDe Wilt, J.G., Van Oosten, H.J., Sterrenberg, L., 2000. Agroproduction Parks—Perspectives and Dilemmas. IEA Bio-energy, 2003,Jansen, J.L.A., 2000. Quality of life, sustainable and world wide: new challenges for agricultural research. In: Boekestein, A., Diederen, P., Jongen, W.M.F., Rabbinge, R., Rutten, H. (Eds.), Towards an Agenda for Agricultural Research in Europe. Wageningen Pers, The Netherlands, pp. 227–237 [ISBN 90-74134-80-7]. Kasse, D., 2002 (personal communication). Hoofdproductschap Akkerbouwgewassen. The Hague, The Netherlands (average of recent 5 years EU Fibre flax production data).
J.E.G. van Dam et al. / Industrial Crops and Products 21 (2005) 129–144 NOVA Institut., 1996. Das Hanf-Produktlinien Projekt. DBU-Projektnummer 07956, K.ln, Germany. Rexen F., Bagger, C., 2002. Potentials for New High Tech Applications of Carbohydrates, Proteins, and Fibers from Oilseed Meal. In: Proceedings of the AOCS World Confernces and Exhibition Oilseed and Edible, Industrial and Speciality Oils, 12–15 August 2002, Istanbul, Turkey. Sessa, D.J., Willett J.L. (Eds.), 1998. Paradigm for successful utilization of renewable resources. AOCS Press, Champaign, IL. Shell International, 2001. Energy Needs, Choices and Possibilities—Scenarios to 2050, Global Business Environment. Schl..er, T., Knothe, J., 2000. Entwicklung naturfaserverst.rkter Kunststoffbauteile für das Kfz-Inetieur und – Exterieur. Bioresource Hemp 2000, 13–16 September 2000, Wolfsburg, Germany. Spelman, C.A., 1994. Non-food uses of agricultural raw materials, CAB International, Wallingford, UK [ISBN 0 85198 769 9]. Struik, P.C., Rabbinge, R., Van Kemenade, M.J.J.M., 2001. Naar effici.nte ketens van biomassa. Chemisch 2Weekblad 16, 14– 15. Van Dam, J.E.G., Van Vilsteren, G.E.T., Zomers, F.H.A., Hamilton, I.T., Shannon, W.B., 1994. Study on: increased application of domestically produced plant fibres in textiles, pulp and paper production and composite materials, Industrial Fibre Crops (EC DGXII—EUR 16101 EN). Van Dam, J.E.G., 1999. Optimisation of methods of fibre preparation from agricultural raw materials. Natural Fibres Performance Forum, IENICA Conference, 26–27 May 1999, Copenhagen, Denmark. Van Dam J.E.G., Elbersen H.W., Van Doorn J., 2000. Cascade use of verge grasses for ‘green’ chemicals and energy. In: Proceedings of the First World Conference on Biomass for Energy and Industry Conference, 5–6 June 2000, Sevilla, Spain. Van Dam J.E.G., Elbersen, W., 2003. In: R.M. Goodman (Eds.), New Industrial Crops in Europe. Encyclopaedia of Plant and Crop Science. Marcel Dekker, 87–96. Van Tuil, R., De Jong, E., Scottt, E., Weusthuis, R., Vellema, S., De Keizer, I., Croezen, H., 2002. Biomass for the chemical industry. ATO/CE Report. USDA/AARC, 2000. Life cycle studies on hemp fibre reinforced components and ABS for automotive parts. Angew. Makromol. Chem. 272, 121–127. #p#分页标题#e#