1. Supply Chain
1.1 Supply Chain Concept
One of the most significant paradigm shifts of modern business management is that individual businesses no longer compete as solely autonomous entities, but rather within supply chains. The term “supply chain management” arose in the late 1980s and came into widespread use in the 1990s. There are many definitions of supply chain, depending on the viewpoint of the definer. Some definitions are offered below:
• “A supply chain is a network of facilities that procure raw materials, transform them into intermediate goods and then final products, and deliver the products to customers through a distribution system.” — from Lee and Billington, 1993
• “A supply chain is a network of facilities and distribution options that performs the functions of procurement of materials, transformation of these materials into intermediate and finished products, and the distribution of these finished products to customers.” — from Ganeshan, Ram, and Terry P. Harrison, 1995, “An Introduction to Supply Chain Management”
• “A supply chain is the alignment of firms that bring products or services to market.” — from Lambert, Douglas M., James R. Stock, and Lisa M. Ellram, 1998, Fundamentals of Logistics Management, Boston, MA: Irwin/McGraw-Hill, Chapter 14
• “A supply chain consists of all stages involved, directly or indirectly, in fulfilling a customer request. The supply chain not only includes the manufacturer and suppliers, but also transporters, warehouses, retailers, and customers themselves.” — from Chopra, Sunil, and Peter Meindl, 2001, Supply Chain Management: Strategy, Planning, and Operations, Upper Saddle River, NJ: Prentice-Hall, Inc. Chapter 1
• “A supply chain consists of supplier/vendors, manufacturers, distributors, and retailers interconnected by transportation, information and financial infrastructure. The objective is to provide value to the end consumer in terms of products and services, and for each channel participant to garner a profit in doing so.” — from Shain & Robinson, 2002
The paper follows the last one in the list above, the definition of supply chain from Shain & Robinson. By understanding the definition, it is identified that there are some key components required in a supply chain.
1. Network
Synonym of “chain” and “system”; emphasizes the fact that participants in the supply chain are specialized and interdependent.
2. Entities
It’s the term for various stakeholders in the supply chain, such as supplier/vendors, manufacturers, distributors, and retailers. They may also be called players, participants.
3. Complementary assets
The labor among participants contribute specialized, mutually supporting resources (skills, tools) to the supply chain; the facilities such as distribution centers, warehouses, etc. All of which are needed for the supply chain to fulfill its mission.#p#分页标题#e#
4. Linked or shared processes
Encompasses all processes required and decisions made to procure raw materials, transform them into intermediate and finished goods, distribute the finished goods to customers, and provide after-sales service; involving flows of information, materials and funds, these processes are linked or shared since they form the continuum of economic activities necessary to meet consumers’ needs
5. Customers
The ultimate buyers who consume the goods or services
Each supply chain has its own unique set of market demands and operating challenges and yet the issues remain essentially the same in every case. Companies must make decisions individually and collectively regarding the key components to develop their supply chain.
1.2 Supply Chain Management Concept
The SCM concept could be said to consist of five distinct management stages. The first can be described as the era of internal logistics departmentalism. In the second stage, logistics began the migration from organizational decentralization to centralization of core functions driven by new attitudes associated with cost optimization and customer service. Stage three witnessed the dramatic expansion of logistics beyond a narrow concern with internal warehousing and transportation to embrace new concepts calling for the linkage of internal operations with analogous functions performed by channel trading partners. As the concept of channel relationships grew, the old logistics concept gave way, in stage-four, to full supply chain management. Today, with the application of internet technology to the SCM concept, we can describe SCM as entering into stage five, e-SCM. These stages are portrayed in Table
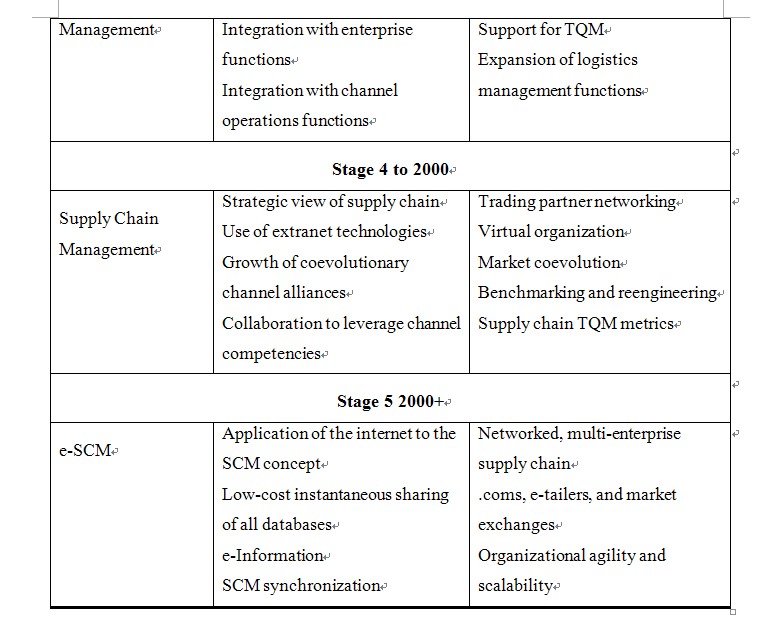
1.3 The Role of Physical DCs in Supply Chain
There are a number of reasons why DCs are required. These vary in importance depending on the nature of a company's business. In general, the main reasons are:
• To hold inventory and decouple demand requirements from production capabilities. This helps to smooth the flow of products in the supply chain and assists in operational efficiency, enabling an 'agile' response to customer demands.
• To hold inventory to enable large seasonal demands to be catered for more economically.
• To hold inventory to help provide good customer service.
• To enable cost trade-offs with the transport system by allowing full vehicle loads to be used.
• To facilitate order assembly.
These reasons emphasize the importance of the DCs. It is possible to summarize the main reason for developing a logistics network as ‘the need to provide an effective service to the customer, whilst minimizing the cost of that service’. Service and cost factors are thus of paramount importance when determining the number, size and location of DCs.#p#分页标题#e#
For the best possible customer service, a DC would have to be provided right next to the customer, and it would have to hold adequate stocks of all the goods the customer might require. This would obviously be a very expensive solution.
At the other extreme, the cheapest solution would be to have just one DC and to send out a large truck to each customer whenever his or her orders were sufficient to fill the vehicle so that an economic full load could be delivered. This would be a cheap alternative for the supplier, but as deliveries might then only be made to a customer once or maybe twice a year, the supplier might soon lose the customer's business.
There is obviously a suitable compromise somewhere between these extremes. This will usually consist of the provision of a number of DCs on a regional or area basis, and the use of large primary (line-haul) vehicles to service these, with smaller vehicles delivering the orders to customers. For certain operations, of course, even these simple relationships will vary because of the need for very high levels of customer service or the very high value of products.
In addition, it should be noted that there are a number of different types of DC, each of which might be considered in a suitable physical distribution structure. These might include:
• Finished Goods DCs — these hold the stock from factories;
• Distribution Centers, which might be central, regional (RDC), national (NDC) or local DCs — all of these will hold stock to a greater or lesser extent;
• Trans-shipment sites or Cross-docking DCs — by and large, these do not hold stock, but act as intermediate points in the distribution operation for the transfer of goods and picked orders to customers;
• Seasonal stock-holding sites;
• Overflow sites.
Logistics network and DC location strategies are aimed at establishing the most appropriate blend of storage and transport at a given customer service level. The interrelationship of the different distribution elements and their associated costs thus provide the basis for decision making.
1.3.1 The Cost Factor
The overall logistics cost is the cost should be taken into account, which varies with respect to the different site alternatives (number, size, type and location), and consists of the individual distribution cost elements.
1. Production Costs
These will vary according to the type of production process or system used and the type of product manufactured. Make-to-stock or make-to-order will also be relevant. Factories may be 'focused' on one or two specific types of product or may make a large range of different products. Different distribution structures may be required to support different types of product. The effect on primary transport costs will be very relevant.
2. Packaging Costs
These are mainly concerned with the trade-off between the type of packaging and the handling and transport costs. The type of load unitization will also be important.#p#分页标题#e#
3. Information Systems Costs
These cover a wide area from order receipt to management information systems. The type of DC network will affect many of these costs. These costs may represent a variety of information or communication requirements ranging from order processing to load assembly lists.
4. Lost Sales Costs
These might occur because of inadequate customer service, and are very relevant in the context of the proximity of the DC to the customer, together with the reliability and speed of service.
5. Inventory Costs
These include the cost of capital tied up in inventory as well as the cost of obsolescence, etc. They have a fundamental relationship with the DC network in terms of the number of stock-holding points and the hierarchy of stock-holding according to DC type.
The key costs can be broken down into four main areas:
• Capital cost — the cost of the physical stock. This is the financing charge, which is the current cost of capital to a company or the opportunity cost of tying up capital that might otherwise be producing a return if invested elsewhere.
• Service cost — that is, stock management and insurance.
• Risk costs — which occur through pilferage, deterioration of stock, damage and stock obsolescence.
• Storage costs — here considered separately as warehousing costs.
6. Transport Costs
The number and location of sites within the distribution structure, and the associated throughputs significantly affect transport costs. Both primary transport and final delivery costs are affected by DC numbers and location.
The two most important categories of transport costs are primary (trunking/linehaul) and secondary (final) delivery. These are affected differently according to the number of DCs in a distribution network.
Delivery transport is concerned with the delivering of orders from the DC to the customer. This can be carried out by a company using its own fleet of vehicles or by a third-party carrier. Whichever alternative is used, the cost of delivery is essentially dependent on the distance that has to be travelled. Delivery distance can be divided into two types: 1) 'drop' distance, which is the distance travelled once a drop or delivery zone has been reached; and 2) 'stem' distance, which is the distance to and from a delivery zone. Whilst the 'drop' distance remains the same whatever the distance from the supplying DC, the 'stem' distance varies according to the number of DCs in the system. The greater the number of sites, the less the stem distance.
The primary transport element is the supply of products in bulk (i.e. in full pallet loads) to the DCs from the central finished goods warehouse or production point. Once again, the number of sites affects the overall cost of this type of transport. In this instance, the effect is not a particularly large one, but it does result in an increase in primary transport costs as the number of DCs increases.#p#分页标题#e#
If the costs for both primary and delivery transport are taken as a combined transport cost then the total transport costs can be related to the different number of DCs in a distribution network. The overall effect of combining the two transport costs is that total transport costs will reduce, the greater the number of sites that there are in the system.
7. Warehousing Costs
These costs vary according to the type of storage and handling systems used, together with the volume and throughput at the site. The size and type of site will thus be important, as will the location.
The major cost breakdown is between building, building services, labour, equipment and management/supervision. The relationship of these costs will, of course, vary under different circumstances — industry, product type, volume throughput, regional location, age of building, handling system, etc. In general, the direct labour cost is likely to be the greatest element, with the building cost likely to fluctuate from very high (new building, prime location) to very low (old building, peppercorn rent, low rates or local taxes).
1.3.2 The Customer Service Factor
Customer service, as a critical success factor for most companies, has become very significant. But the ability to improve service levels and to maintain this improvement is a challenge that faces many companies. The major reasons are:
• the growth in customer expectations — thus service fulfillment has become a priority for any successful strategy;
• the growing professionalism of buyers — many buyers now recognize the importance of service as well as price in the product offering;
• markets have become increasingly service-sensitive — there is little else to differentiate between products;
• the diminution of brand loyalty, particularly with respect to FMCG, where immediate product availability is the vital factor;
• the development of new ideas such as relationship marketing where fulfilling service expectations is the key and customer retention is a priority.
The components of customer service may be seen as transaction-related elements, where the emphasis is on the specific service provided. They are usually divided into three categories. These reflect the nature and timing of the particular service requirements (before, during and after delivery of the product):
1. Pre-transaction elements: these are customer service factors that arise prior to the actual transaction taking place. They include:
• written customer service policy;
• accessibility of order personnel;
• single order contact point;
• method of ordering;
• order size constraints;
• system flexibility;
2. Transaction elements: these are the elements directly related to the physical transaction and are those that are most commonly concerned with distribution and logistics. Under this heading would be included:#p#分页标题#e#
• order cycle time;
• order preparation;
• inventory availability;
• delivery alternatives;
• delivery time;
• delivery reliability;
• delivery of complete order;
• condition of goods;
• order status information.
3. Post-transaction elements: these involve those elements that occur after the delivery has taken place, such as:
• availability of spares;
• invoicing procedures;
• invoicing accuracy;
• product tracing/warranty;
• returns policy;
• customer complaints and procedures;
• claims procedures.